Model Building Process
Let’s introduce a modeling building process called LEAP. This is the strategy used to build a simulation model in Process Simulator or ProModel/AutoCAD.
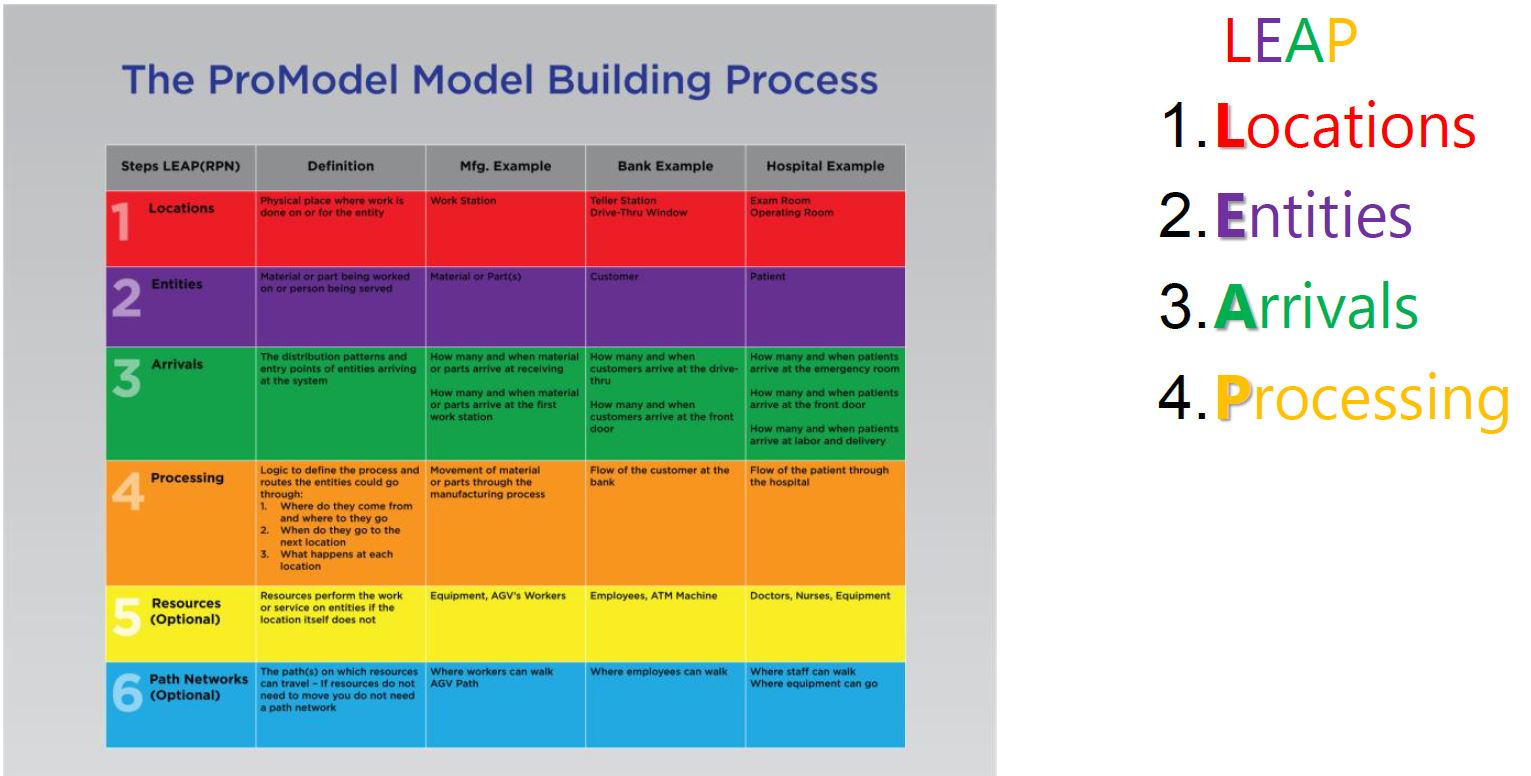
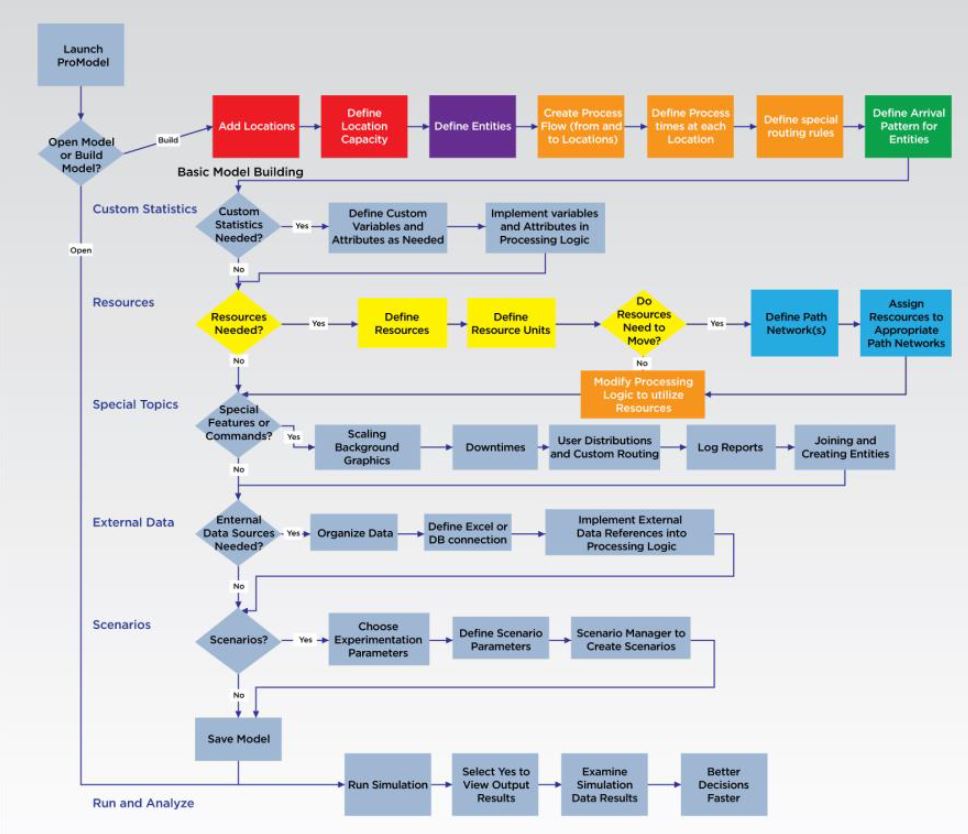
Create a simulation model with Factory Design Utilities that opens directly in AutoCAD/Inventor to start a factory layout
To build models and take advantage of the Autodesk integration, you must have Microsoft Visio installed in order to use Process Simulator, and you must have Autodesk’s AutoCAD, Inventor, and Factory Design Utilities installed. Now let’s see how to build a simple model from scratch in Process Simulator.
Process Simulator Workflow and Integration
- New process design and layout or change the current process and/or layout
- In Process Simulator:
- Start with a blank page
- Lay Factory Assets into model (locations)
- Define additional resources and constraints (operators, MHE)
- Define product mix (entities)
- Define process flow (routings)
- Define parameters for experimentation
- Define key performance metrics and reports
- Set up and run simulation scenarios of process/layout options
- Analyze reports to identify the best process/layout options
- Open in or export to AutoCAD/Inventor