Showcasing the Stavanger University Hospital in Norway, this article will introduce new workflows in Revit for the seamless design of cross-discipline modular and prefabricated components. The Scandinavian hospital proposes a giant lego-like assembly in its construction and tests new workflows and Revit functionalities to enable the efficient control and development of the prefabrication strategy parallel to the overall project design.
We will present an interdisciplinary BIM workflow for the drawing and analysis of prefabricated modules and show new techniques in data management which have allowed us to monitor component changes, identify deviations, and align project outputs with the information demands of the building industry. We will also demonstrate how this methodology can be applicable to schools, hotels, and other repetitive or prefabricated projects.
The Project: The Stavanger University Hospital (SUS 2023)
The Stavanger University Hospital project proposes a 100,000-square-meter first phase with a dedication to providing high quality hospital and research facilities within the allocated budget, with on-site completion in 2023. The site lies adjacent to green areas and its four main buildings are situated around a central court with collective transportation routes along a main axis. The buildings are connected through an underground culvert and a continuous ring of glass bridges on the second and third floors.
Presenting from the AU Theater stage, Kristoffer Tungland and Eva Eriksson share how firms collaborating on the Stavanger University Hospital project pioneered a new modular construction approach to increase efficiency, control cost, and reduce risk.
The hospital provides emergency, helicopter, and operation facilities, bedroom wards in three of the buildings, and well-allocated spaces for staff and visitors. Its 628 bedrooms are all single occupant with suites, and with central atriums in each building, with the connection to nature and natural daylight prioritized for enhanced patient recovery. The project is standardized to the greatest extent possible for good patient safety, flexible use, and functions that will be easy to change in the future.
The project team consists of two architecture firms, Nordic Office of Architecture and AART; two structural firms, COWI and Aas Jakobsen, MEP: COWI; and landscape architects SLA.
Related: Integrated BIM Workflows in Modular Prefabricated Construction: Concept to Fabricate with Bimal Patwari and Scott Pittman

Site plan of SUS. The buildings are positioned around a square with a collective axis and connected by a ring of glass bridges on the second and third floors.

Project BIM Delivery
The project’s ambition for efficiency through digital-based communication led to a high level BIM strategy from the early phases. This delivery currently includes the following:
- All disciplines delivering full BIM models in IFC (exports from Revit, Tekla, Civil 3D)
- Wind analysis
- Full analytical analysis and airflow analysis
- Energy analysis, daylight analysis, environmental performance analysis
- Synchronization with room database (dRofus)
- Quantity take off from sketch phase
- Area control
- Augmented reality (Oculus Rift with Revizto and Enscape)
- BIM cave
- Object status
- Crash control
- BIM model connection to critical path — construction simulation
- Paperless
- Model connection to PIMS/Safran

Project File Structure
In the conceptual phase, project files were divided up as follows due to size. The delivery file format for this type of project is, in Norway, determined by the government, which stipulates that all projects are exported to IFC.

SUS 2023 — The Conceptual Phase
Early Evidence of Repetition
Due to the nature of the project, repeating geometry is abundant, and in the early phases grouping in Revit provided the opportunity for most disciplines to increase the effectiveness of modelling duplication.
This type of element repetition can be substantially different per discipline. For example, for the architects: the repetition of hospital bedroom/bathroom layouts, and MEP: duplicate system solutions per zone and repetition of outlets and light fixture placement.

There are pros and cons to the use of groups to model repeating design and due to the complexity of evolving alternative layouts in the conceptual phase and the need for consistently accurate quantification, many architectural groups were reduced or separated to “furniture” room groups and one-sided room grouping.
If you are planning to use groups for repeating design in the early phases, consider your team structure and deliveries and make an organization strategy.

One of the major benefits of grouping repeating design is the existence of a local base point within the group allowing the switching in and out of different solutions by aligning these points. With this we can also create a library of layouts for future use.

Note: Only one person can work on one group at a time resulting in reduced collaboration, and if using design alternatives, groups must be modelled cleanly as intersecting geometry will cause problems in their interaction with main model elements.
The Evidence of Repetition in the Façades
With 50,000 square meters of façade area, façade repetition was also a key area for advantageous modelling strategies. In the initial concept phases, the facades were quantified traditionally and drawn using curtain wall workflows, taking advantage of the duplication of singular material panels by using global parameters and intelligent curtain wall types.
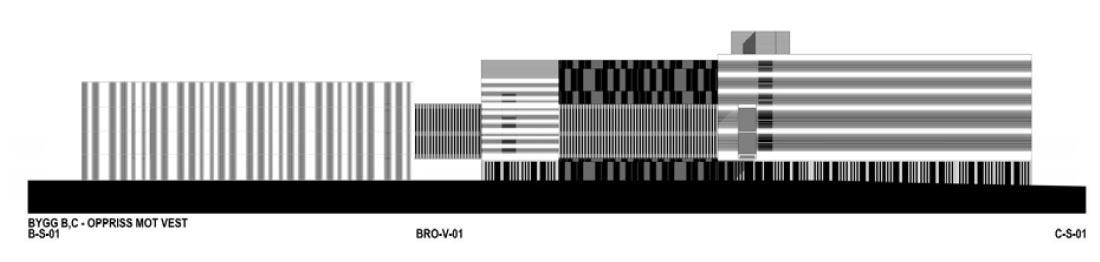
SUS — The Developed Design Phase
The Introduction of a Modular Strategy
The project, after completing the initial conceptual phases with traditional build quantification, moved forward with the concept of an industrialized construction strategy.
Why Industrialized?
Besides cost, quality assurance, standardization, and increased building efficiency, innovation using industrialization is the perfect fit for SUS due to a recent downturn in local oil production. This has resulted in many highly skilled engineers and industry workers left unemployed. Using the fabrication expertise from the Stavanger oil industry, the project together with the available workforce has become a highly effective collaboration.
Designing the Strategy
To assess the project for possible areas for industrialization, the project went through a “potentials map” design process. The potentials map was populated with opportunities but also defined by constraints coming from both local and project based factors. Some examples include:
- The limitation in the transportation size of elements in Norway restricting module dimensions
- The use of medical gas meaning certain systems can never be part of modules (regulations for installation and the joining of parts)
- A client-approved design layout meaning the modulation strategy could not create additional structures appearing in undesired locations

To legitimize the buildability of the modulation strategy after the potentials map assessment, the project involved industrialization professionals Bryden Wood. Bryden Wood currently have active projects involving innovative modular workflows, and use BIM actively for project projection analysis and accuracy in the breakdown of parts.
Improving the Efficiency of Repetition Using BIM
This type of construction strategy highlighted an already identified potential for better control of repeating parts in Revit. It also created the need for cross-discipline information specifically tied to the modulation strategy.
After a series of meetings and workshops with Autodesk and prefabrication experts Project Frog, we formed a BIM process development plan to: ‘Design BIM workflows for the seamless development of cross-discipline modular and prefabricated components in parallel to the overall project.’
Process Development Objectives:
- Enable more efficient cross-discipline control and analysis of the modulation strategy
- Take better advantage of duplication
- Present the modulation strategy through open platform file format (IFC)
- Align project outputs to the information demands of the building industry and produce the right level of information at the right time
- Take control over modular construction sequencing
Whilst:
- Upholding the demands of the design deliveries and full visualization
- Upholding the demands for full project analysis
- Maintaining a workflow that is suitable and accessible to all users
The Result: An Industrialized Approach to Revit
New Team Organization, Responsibility Structure — The project created a dedicated responsibility structure for the modulation strategy. In addition to the per building responsibility structure, modulation team members were given a per module responsibility and a dedicated module BIM manager.
Module Type-List — A type-list formula was established to ensure both panel and module organization within the model, and this system of categorizing would be translatable to the building industry.

Technical Application — Due to the importance and speed of the industrialization information flow (both between disciplines and to the building industry), the module and panel duplication is prioritized over the evidence of design repetition. However, the same workflow can be used for repeating design layouts in similar types of projects. The resulting industrialization of the model is divided in two parts due to differing workflows: modules and façade panelization.
1. Modules
In response to the concepts of our “industrialized BIM” objectives, the SUS MEP engineers developed an add-in coordination tool to Revit based on a dynamo script with a simplified interface, and the BIM team developed a corresponding cross-discipline workflow. The coordination tool understands and controls:
- The position (cross-discipline) of modules in a model
- Relationships between elements in a module
- Parameter values of all elements within modules
- Auditing and tracking of module changes and movements
File Division: The Three File Types
We use three different types of models to create an efficient and collaborative modulation workflow for the team.
A — The Placeholder Model (for conceptual module design)
The placeholder model is a new separated model with instances of ‘placeholder’ elements. These placeholder elements (masses) define the outline and location of project modules — essentially family types with local origins. The placeholder model is uploaded to a central location, and every discipline model has a link to this conceptual module model.

B — Discipline Models (per discipline files — normal working file)
Within the regular discipline file, for every type of prefabrication module, one Revit group will define the discipline part of each module. All disciplines models need to have:
- Split elements so that modules are geometrically separated
- Made one group (or assembly) per module type and named it according to the type-list
- Assigned a group basepoint per module location (these will be in the same locations as the corresponding mass in the placeholder file)
C — Module Model (isolated module files created by saving out groups)
The module model contains individual modules as links from all disciplines — formed by each discipline saving out their module groups as individual files. This file can be used as a complete module for prefabrication. For every type of prefabrication module in the project there exists one unique module model. Groups when saved out can also be edited and reloaded into the discipline file and these files can be used for isolated module development.

The Coordination Tool (automatic placement of modules)
The placeholder model is linked to each discipline model. The coordination tool add-in is designed to search the model or linked models for elements based on a rule set of parameter values and place an object, group, or an assembly on the same place as the found elements (base object). The inserted object has a GUID reference to the base object for monitoring the placement and parameter values.
If a placeholder instance is moved in the placeholder file the module has a monitor on its instance and it knows to be moved to the same place. The interface also brings warnings to accept or reject changes made which do not correspond to the placeholder file.
The location of any module group/assembly can be updated or offset, and their instances altered, replaced or deleted with each deviation being audited, accepted or denied. The tool can also copy and set parameter values to all elements enclosed within the placeholder masses, and this is used to automate the attachment of information to the modulation strategy.

2. Façade Panelization
To align our modelling strategy with the proposed panelization of the façades, the team designed a series of master curtain panel families made up of parametrically editable and nested parts. This has allowed extensive conceptual flexibility, adaptability to per building deviations and accurate quantity take off. Each panel is modelled with all industrialized components included, the module master appearing exactly as it will be produced. The complex type-list allows the separation sorting of modules and module parts for specific information deliveries to the building industry.
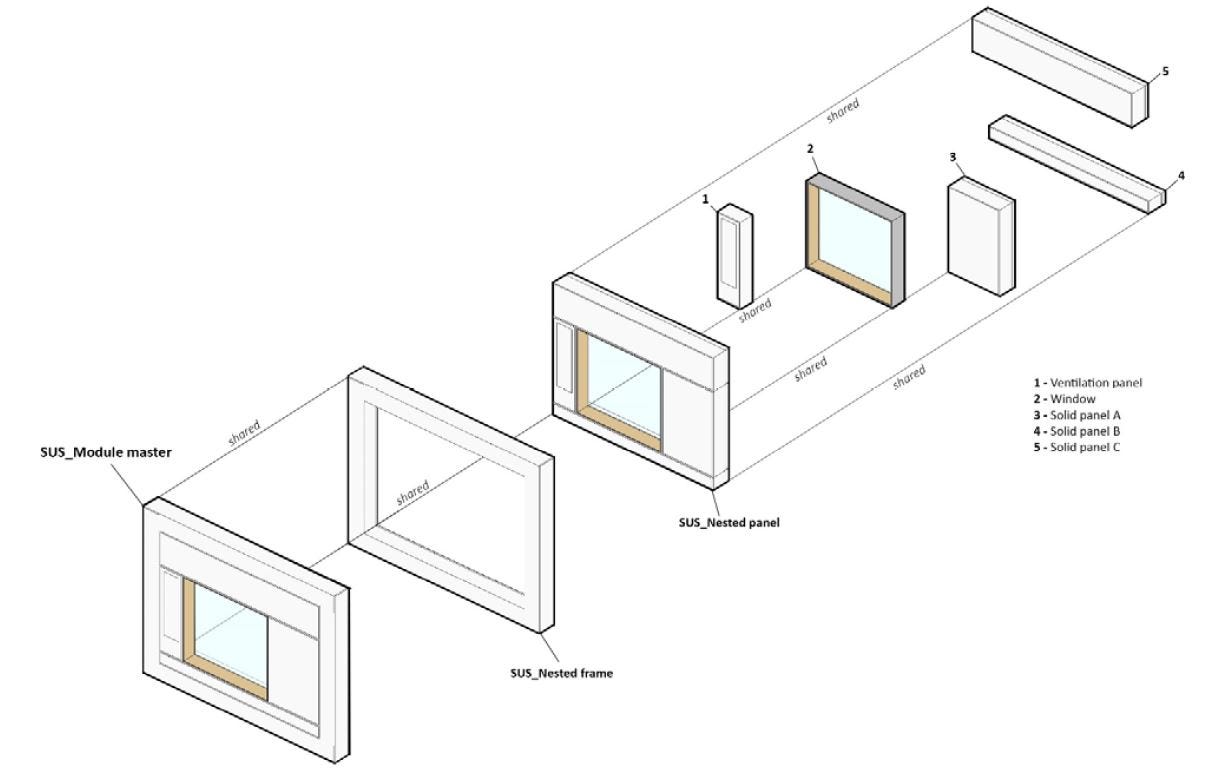

Note: Modelling a curtain panel family with multiple materials (without using nested families) results in incorrect quantities.
Delivery of Industrialized Information to the Building Industry
With the placement of the prefabrication type-list parameter (and any required additional parameters) on modules and on each panel within the façade, we can count, analyze, and translate information connected to the modulation project to the building industry via IFC.
Automized Parameter Placement
Automatization of the parameter placement to elements within modules is done using our coordination tool, and checked through specific filtered views in Revit. In Revit 2018 we also have the ability to tie the parameter to groups as entities and schedule them.
The coordination tool can copy and monitor the module type code and module instance ID from the placeholder family instance to the group and all of its elements members. Note that it’s important to set up the parameters to “values can vary by group instance” to have an instance ID on every element inside a group. Panel parameter placement is type based and checked within the façade file before exporting.
To the Building Industry
Using the type-list parameter values we can create filters and module-specific views in Solibri allowing the efficient and visual communication of the modulation strategy between the project team and the building industry. Using exports from the discipline model and the module models, we can deliver specific information types catered to the needs of the recipients.
Construction Sequence Control
Using the information contained in models, which have been aligned directly with the industrialization strategy, we can connect modules, panels, and all other elements with the critical path and using Navisworks or Synchro simulate the expected industrialized construction sequence, ensuring full control of the assembly before it begins on-site.

Summary
The resulting methodology for cross-discipline industrialization has allowed us to develop a traditional BIM with repeating layouts into a set of modular and panelized components whilst upholding the architectural, analytical, and visualization demands of the overall project. Through automization we have increased our ability to be effective, assure the strategy, allow adaption, and provide appropriate information between disciplines and to the building industry. In adapting to new workflows we aim to better align ourselves with an evolving building industry moving towards manufacturing: the creation and assembly of parts.
Bridget White is originally from New Zealand, and completed an honors degree in Architecture at Victoria University in 2006. After beginning her career working in New Zealand she moved to Norway to start at one of the country’s largest practices, Nordic Office of Architecture. She is an architect, Breeam AP, BIM manager, and BIM coordinator for large-scale airports, hospitals, schools, national governmental facilities, and transportation hubs. She is part of a team of experts at Nordic using a wide range of Autodesk products and implementing new office workflows involving complex analysis, virtual reality, integrated sustainability, and streamlining the flow of information between architects and the building industry.
Kristoffer Tungland started as an electrician and later completed electrical engineering education in Bergen, Norway. He likes to solve and program processes, which are often performed repeatedly, to get a better flow in the design phase. He has experience with the construction process and uses it in combination with programming to solve disciplinary and interdisciplinary challenges. He works daily with customization and an add-in for Revit in the company and for projects.